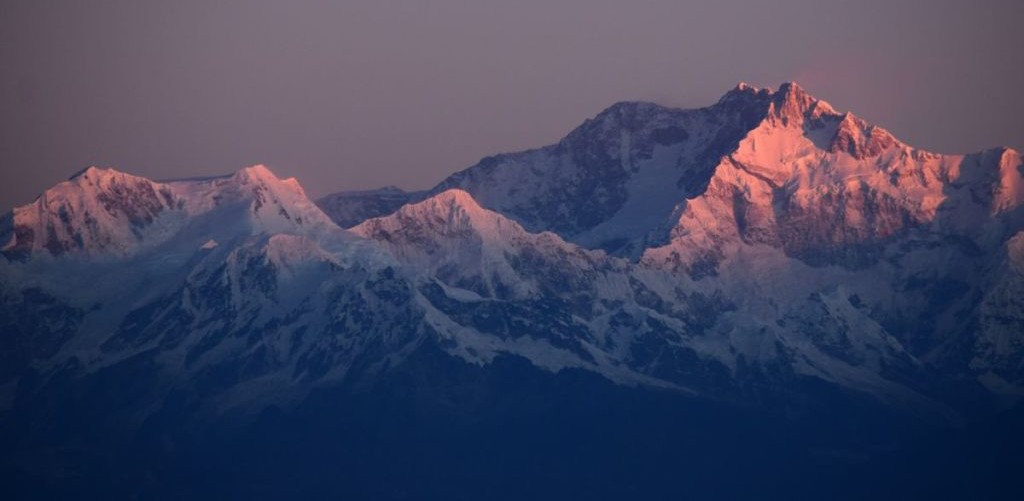
production
Production is amazing! Magic happens when it’s right, but production is a money pit when it’s wrong. Regardless of the product being made, production is a potential minefield! There is both art and science in effective coordination/integration of raw material, machinery, and staffing (there’s people again). Planning, equipment, maintenance, quality, defects or not, call backs or not, par stocks and inventory management, waste, ergonomics, packaging, loading dock/storage, shipment dates, and more are all potential nightmares on any given day.
The Miick wealth of knowledge and experience positively impacts ALL types of production efficiency of any segment in the world of work! We cut our teeth on one of the most complex and volatile manufacturing realms, the restaurant industry, from fine dining to quick service. Restaurants are at their core nothing more than a production plant with cycle time that’s measured in minutes, not days or weeks. For this reason, our experience in restaurant production, focusing on concepts like “just in time,” “zero defects,” or LEAN, has uniquely prepared Miick to bring successful production solutions to all types of industry verticals. Restaurants experience all manufacturing issues every day, and systems developed by Miick maximize performance in them, and translate equally well to the whole, great world of work!
LET’S START A CONVERSATION.
Take your business to new heights. Send us a message and let’s have a discussion.
Let’s Start A Conversation
Take your business to new heights. Send us a message to schedule a complementary consultation with our culture and growth experts.Miick Brings you the “How To” of Efficient, consistent production
Production capacity is a key element that contributes to successfully growing and scaling your organization. The Miick team can help you find your operational sweet spot to maximize profitability, customer satisfaction, and loyalty.
ISSUE: INVENTORY MANAGEMENT
Thinking we’ll be safe and having too much in raw materials or finished goods on hand, and the cost of goods, waste, or shrinkage skyrockets. Too little on hand, not “just in time,” and you can’t produce enough for demand. The ramifications ripple up and down the organization, financial impacts are felt in all departments, customer service suffers, and opportunity costs skyrocket. Strike the band, here comes the “blame game!”
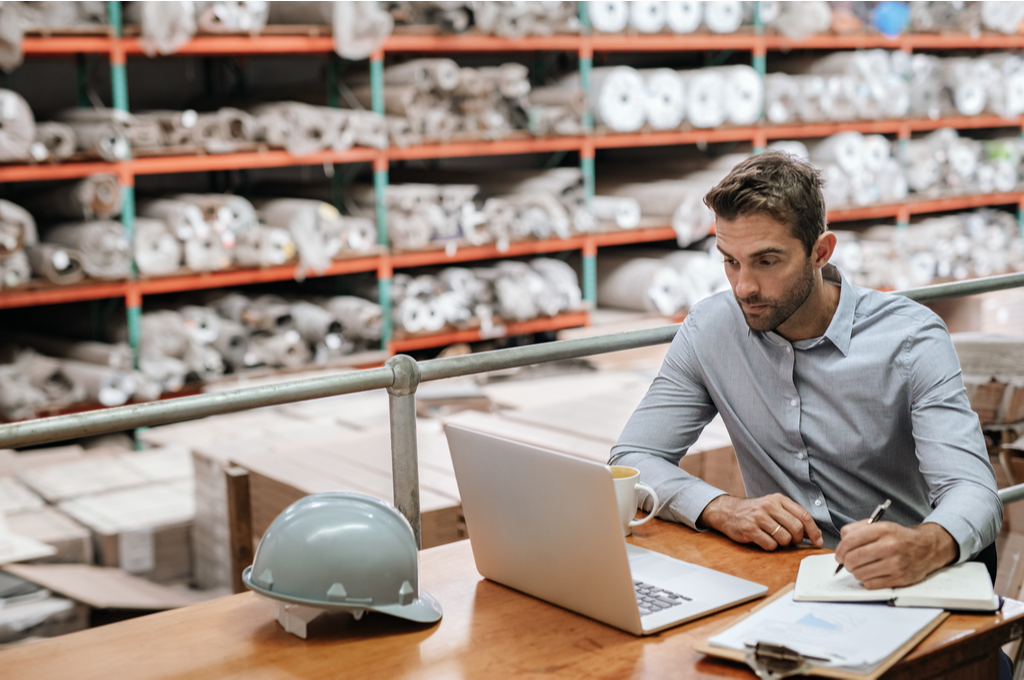
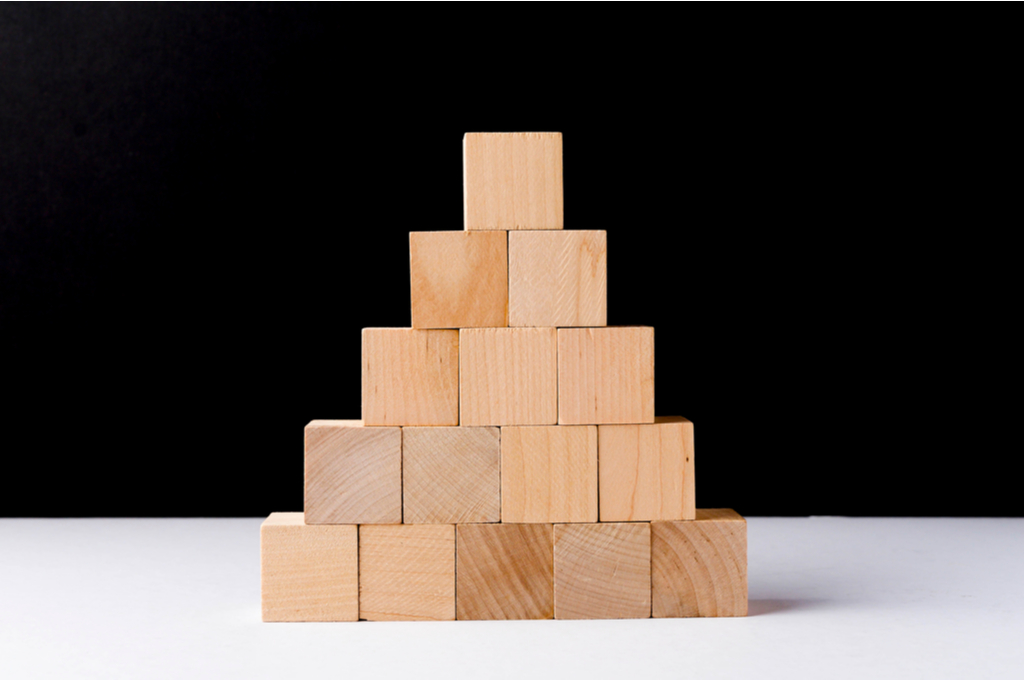
ISSUE: inconsistency
It’s not enough to make a good product once, you’ve got to do it every day! Quality control through finished goods inspection is an expensive approach to doing it right the first time. Businesses need a well-vetted set of “good manufacturing processes” to ensure that, from raw material procurement to finished goods shipping, any glitch can be quickly identified and fixed. Relying on common sense is no solution.
Issue: purchasing/receiving
You didn’t get what you ordered; or you got too much. Nobody checked in the order, pricing is wrong. There isn’t a purchasing budget in the first place, time and again you ballpark and wing it, end up over or short. My managers think the sales people are buddies, “helping” us out. At the end of the day, they’re just selling us stuff, even if we don’t need it. The deal price to get a discount gives us too much inventory on hand, we don’t even have storage capacity. Waste or “shrinkage” goes up. Minimums are killing us! Then there’s long lead times for critical components, and manufacturing’s off. In regulated industries, ensuring compliance to ISO standards and GMP can make finding, managing, and keeping suppliers a challenge. If the external factors aren’t enough, every business has someone who won’t follow internal purchasing policies and systems. Oh, and this issue could go on for paragraphs more! (We know.)
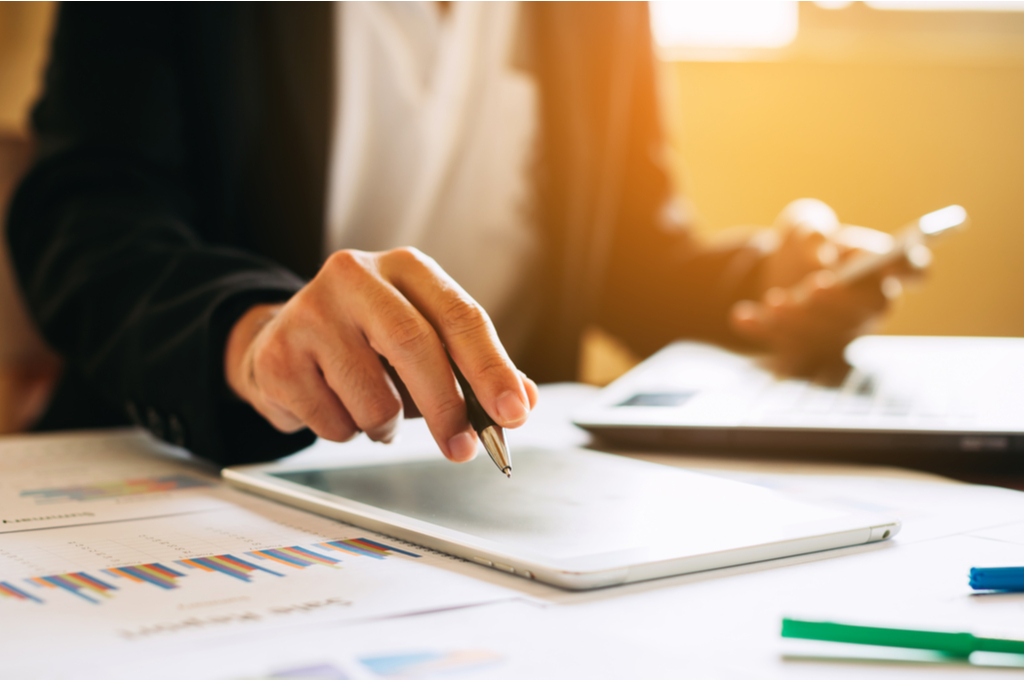
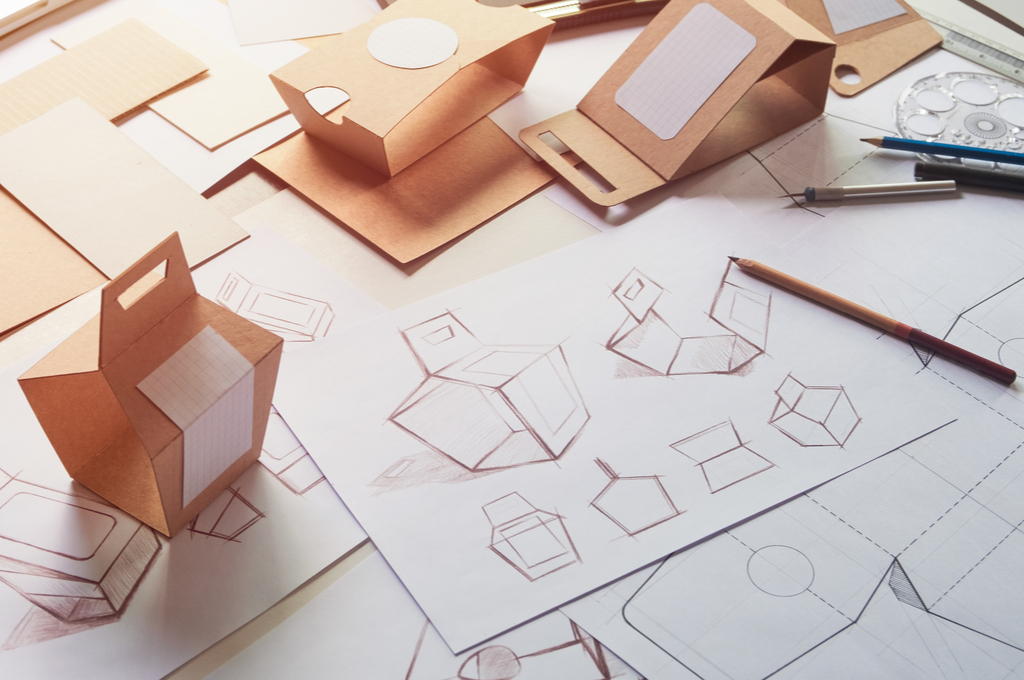
ISSUE: packaging
Packaging, whether a bottle, a box, or the table-side presentation of a gourmet meal has to strike a balance between functionality and the perfect complement to the product itself. No one will buy the product for the package, but they’ll certainly not buy the product if the packaging isn’t right! Packaging and effective completion up to and including delivery, is a core part of the brand experience.
Issue: repair and maintenance
Without clarity of purpose, values, vision, and mission, It’s an oxymoronic to think of repair and maintenance in the same sentence. Ensuring that, as equipment is acquired and put into service, a proactive and comprehensive maintenance schedule is developed and followed is critical to efficient production processes. And, comprehensive, because if one machine or piece of equipment is down, it can affect the entire line. Repairs should be out of the ordinary, while maintenance is part of everyday operations. Have you defined excellence or are you still relying on common sense to maintain or repair?
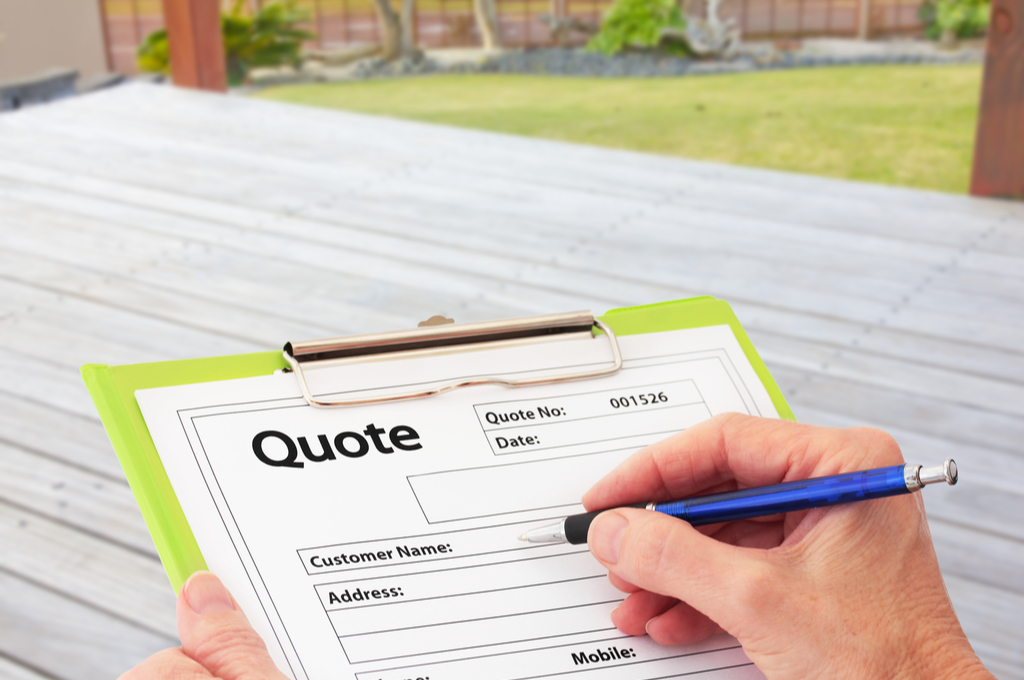
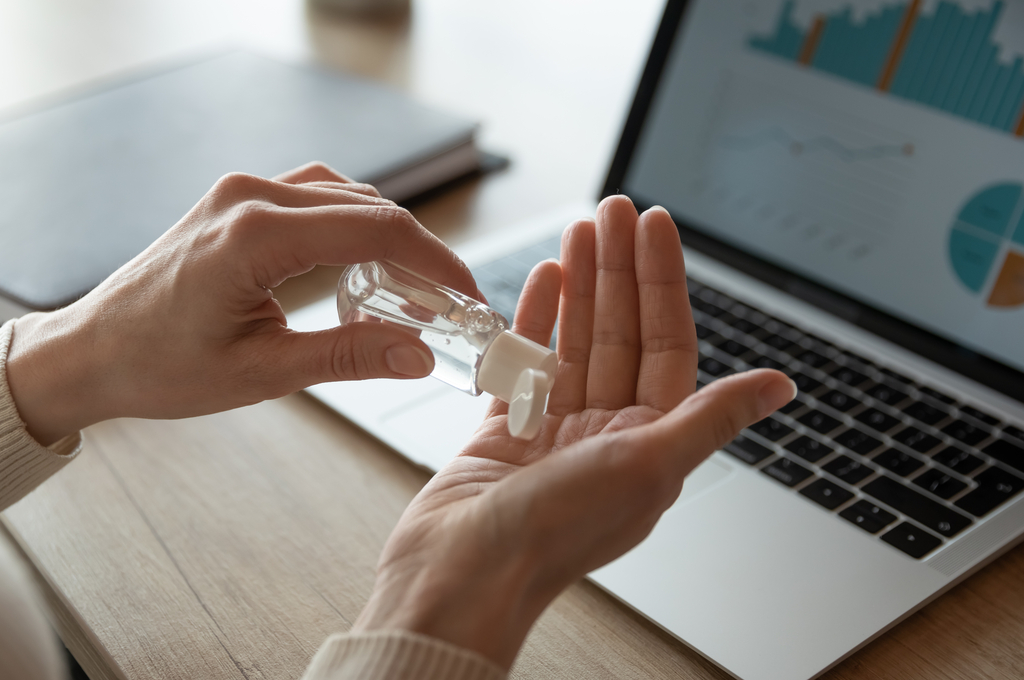
ISSUE: safety and sanitation
2020 was a year to underscore the scope of needs and the importance of compliance to safety and sanitation requirements, regardless of the industry. Depending on the production process, cleaning and sanitizing may be infrequent, but a violation of a regulation can quickly shut the line down until back in compliance. As with maintenance, a comprehensive cleaning scheduled must be developed and followed. On the other hand, safety training and compliance is a daily responsibility of every employee. Lost time injuries are the scourge of any production operation and to be avoided for lost productivity and regulatory issues.
No matter what you are challenged by in production, one of the critical elements will be managing turn times. As with all elements of time in production processes, the key is predictability and consistency. This is particularly true when the turn time is associated with processes outside of the regular production process. Imagine manufacturing aluminum parts requiring anodization, but you don’t complete that process. You’ve got a third-party vendor. The upstream and downstream chaos with unpredictability of turn times from that vendor will completely disrupt your production schedules.
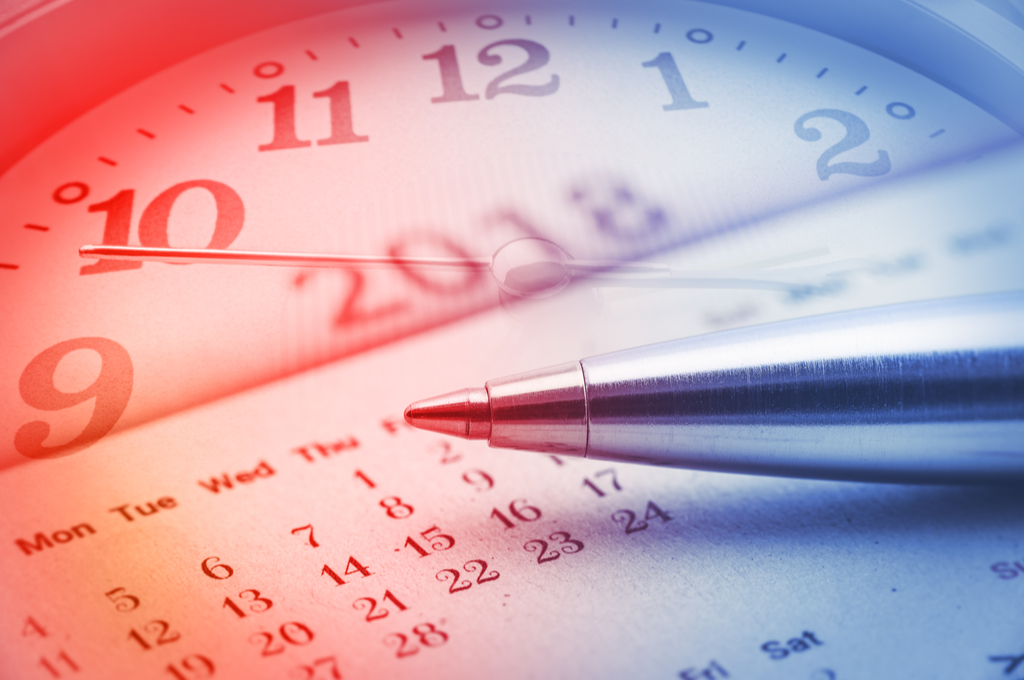
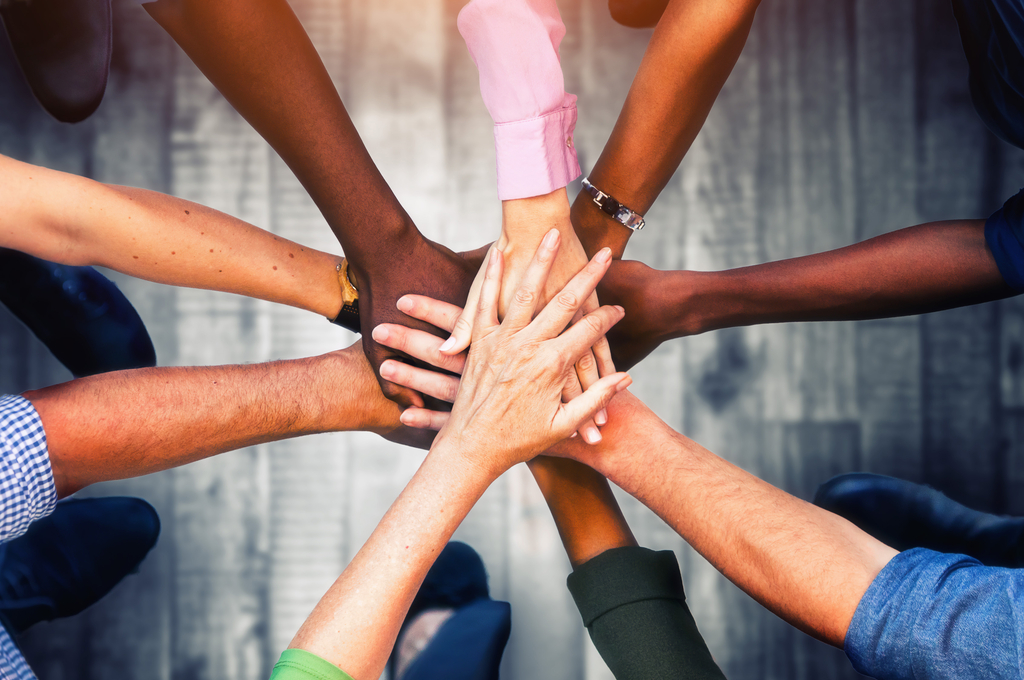
ISSUE: teamwork
You only hire A+ players. You’re a great team builder. You know how to lead a high-performing team. The challenges of teamwork in production should be a snap! They’re not, because the production process brings together a host of teams with individual roles and goals that must all function together in harmony. That’s where a “team of teams” must leverage a team performance model motivated by the good of the whole to deliver for the organization.
Issue: independent work
No way around it, independent work is a mainstay of business, whether a shipping clerk or a CEO, each must find the balance of their unique responsibilities to the fit with the overall organizational goals. The ability of an organization to share collectively in the joy of individual achievement and weave that success into the business wins chalked up each day will propel the organization to higher levels of success. “Individually, we are one drop. Together, we are an ocean.” – Ryunosuke Satoro
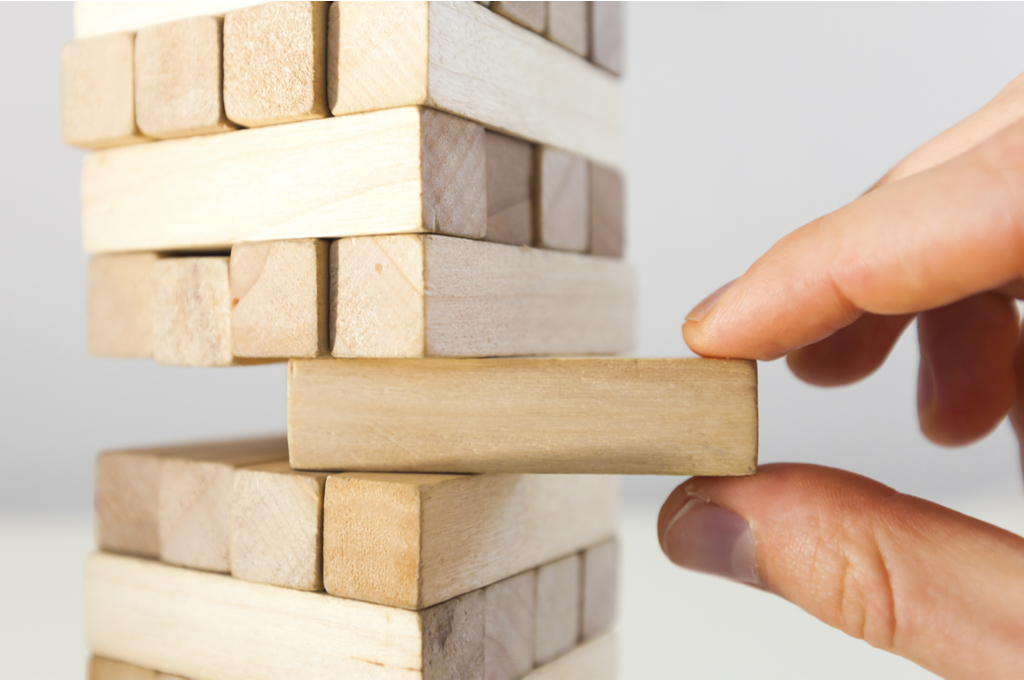
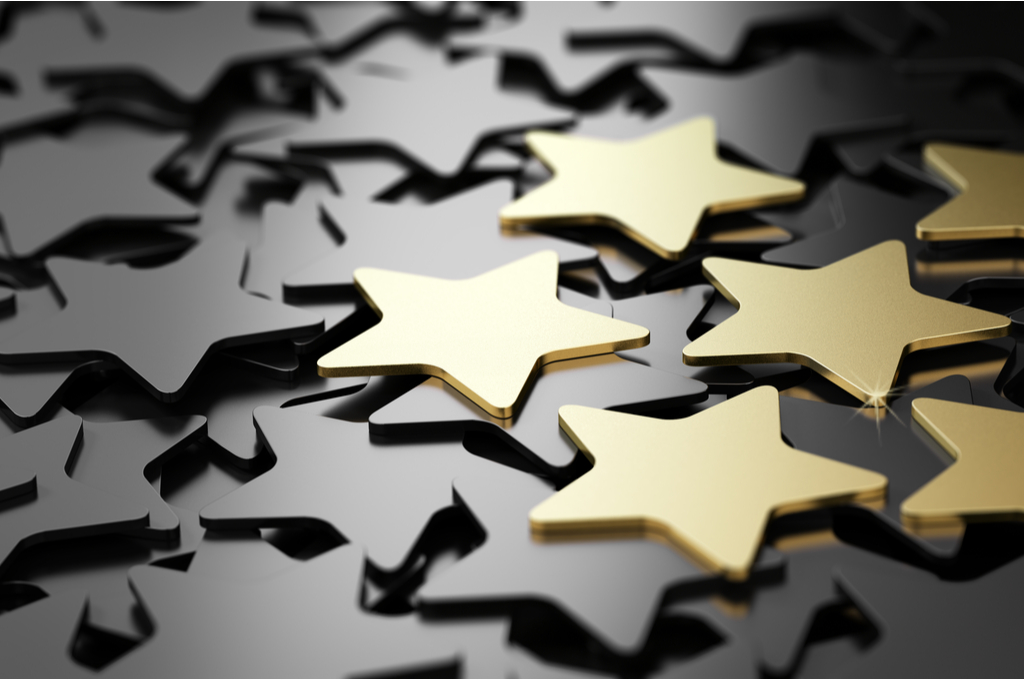
ISSUE: definitions of excellence
Excellence is redefined hundreds of times in our companies. The multitude of business jargon only serves to further complicate achieving a shared definition of excellence. Instilling an ownership attitude in your employees develops a “we” versus “I” culture. Furthermore, being explicit with attitudes and actions, choices made and behaviors observed, A+ performance evolves and grows. What would have been an A+ candidate a year ago wouldn’t even make the team this year. This evolution results in an explicit Culture internally and an explicit Brand Experience focused externally, for customers.
Issue: opening and closing
While more common to retail or restaurant, hours of operation and staffing are challenges the COVID-19 pandemic has brought to the forefront for many business owners. The type of business, type of service, the market you intend to serve, seasonal variations all should be addressed. Common courtesy for the patrons and employees should be the goal, supported by communication and adherence to whatever plan is devised to manage opening hours.
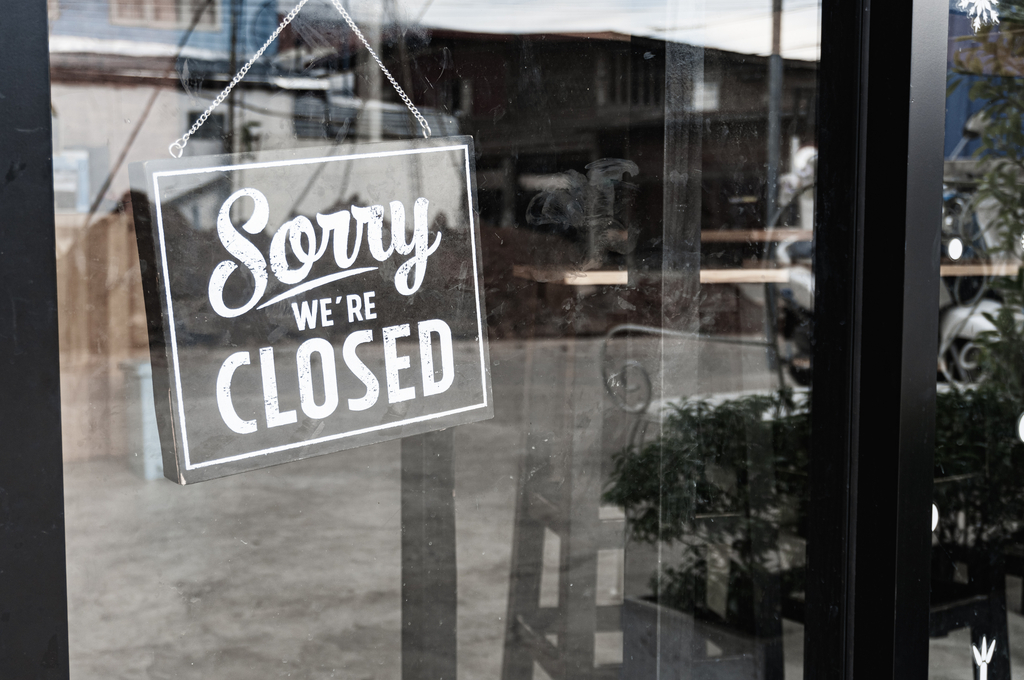
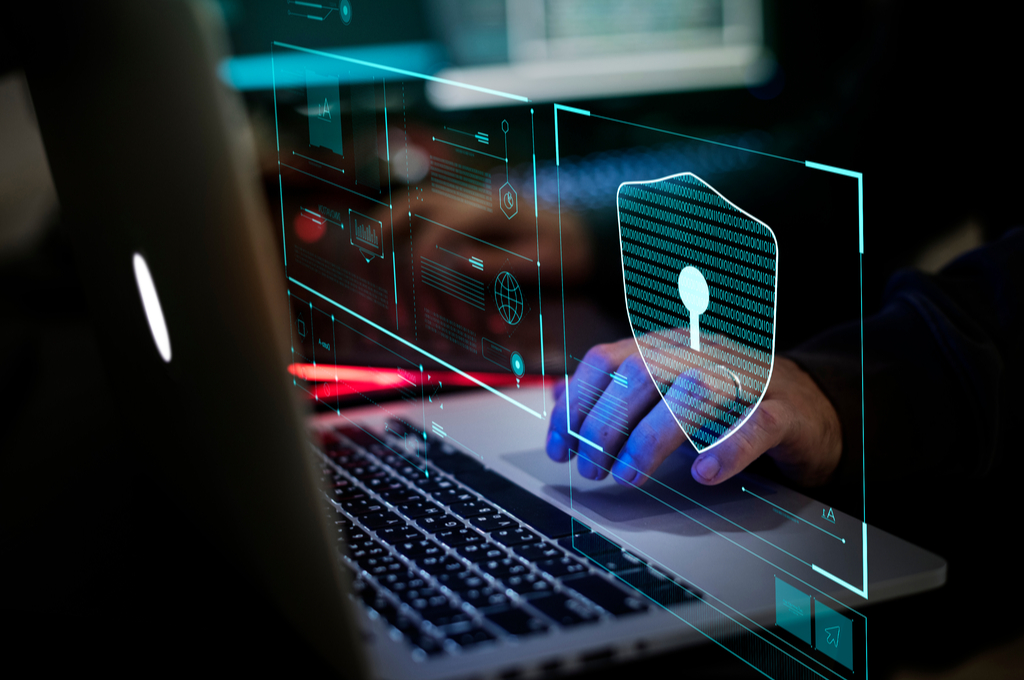
ISSUE: security
Should just be able to lock the doors or hire 24/7 security to ensure the integrity of the production lines, right? From restaurants with complex inventory management and POS systems to full-scale manufacturing facilities with automation at every step of the production process, security goes way beyond “the floor.” All the equipment, all the automation, all the software systems rely on data. Of data espionage across ten major U.S. industry segments, manufacturing represents over 25%. Never before has security been so important to long-term operations and success.
Issue: sales growth
Leaders wanting to achieve sustained growth need to be invested in more than just the short-term fiscal performance of the business. Sure, cash flow will always be king. But leaders need to work with their financial teams to ensure sales, expense, and cash flow projections account for the ebbs and flows of business over longer periods of time. As well, supporting their teams and providing for their growth ensures a valuable ally in the long-term, successful business plan. Taking every opportunity to build the brand as part of the community, versus just the business itself, creates a loyal patronage that sustains growth. Adopting a holistic approach to business growth will greatly improve the chance of success.
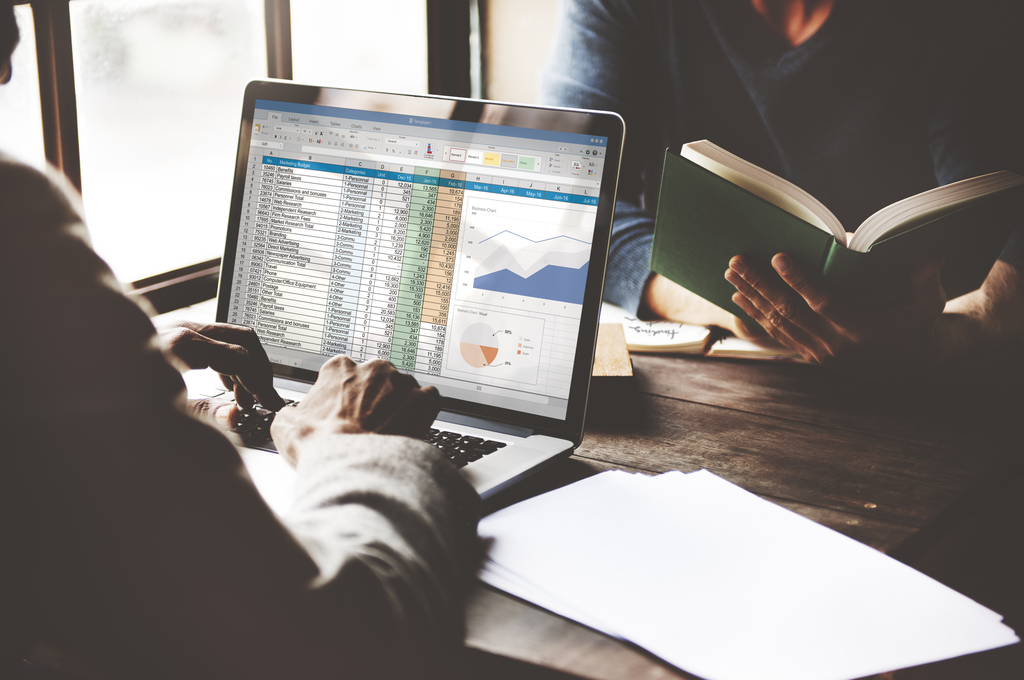
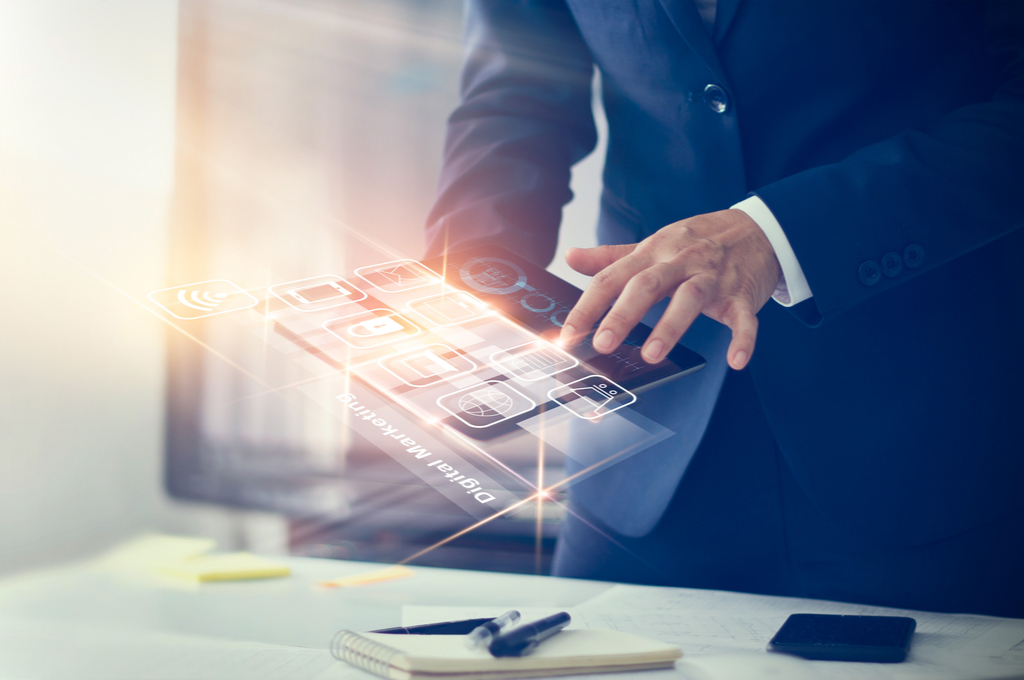
ISSUE: technology
Images of robotic production lines, virtual offices supporting 10 workers to hundreds of workers, a revolution in workflow software and software solutions, the “cloud;” are great examples of technological advances. They do not, however, change the challenges of human interaction. What to buy, what to subscribe to, how to scale, who will train, how to plan for obsolescence, what are the back-ups? All challenges that must be addressed in the integration of technology with the workforce. What is certain is, the technology we use today will, most likely, be different in five years!
You can pretend that if the whole team could just be exposed to the same information in the same way, communication would be easy. Sadly, this is the whole point of missed communication. There are a myriad set of tools and ways in which to communicate. Sadly, more often than not, managers and leaders use innuendo, compliments or “constructive” criticism to guide performance. This is a path to drama, finger pointing, reasons, stories and excuses and potentially to harassment or hostile work environments named as “unfair” or worse. Communication is the primary “HOW TO” of getting work done well. Miick delivers BIG solutions here with communication training built on a no drama work environment, and “feedback to the positive.”
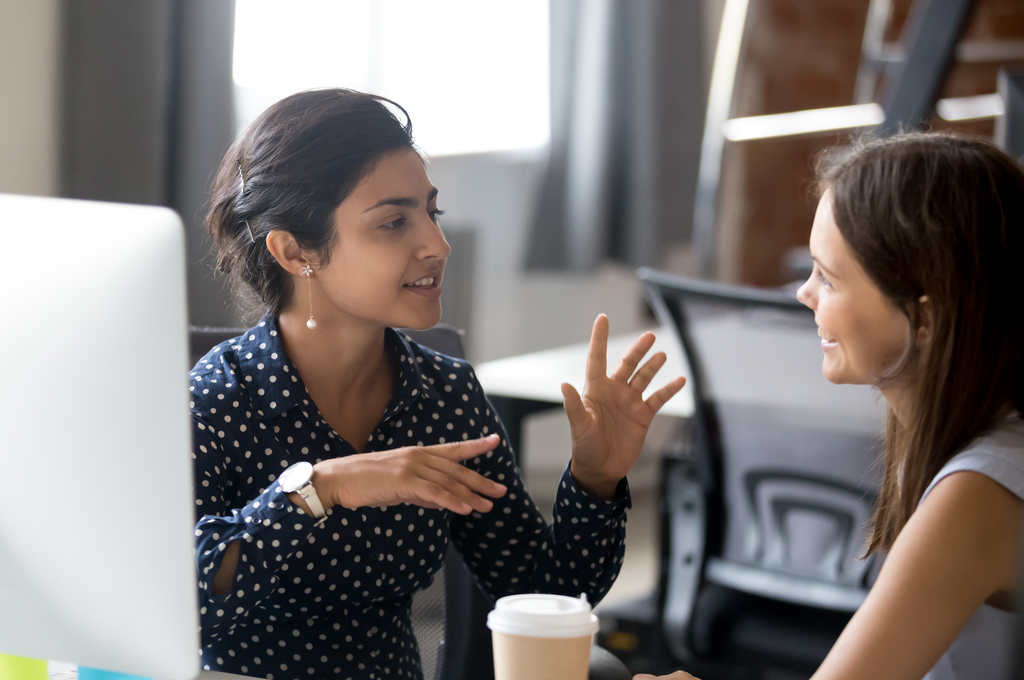